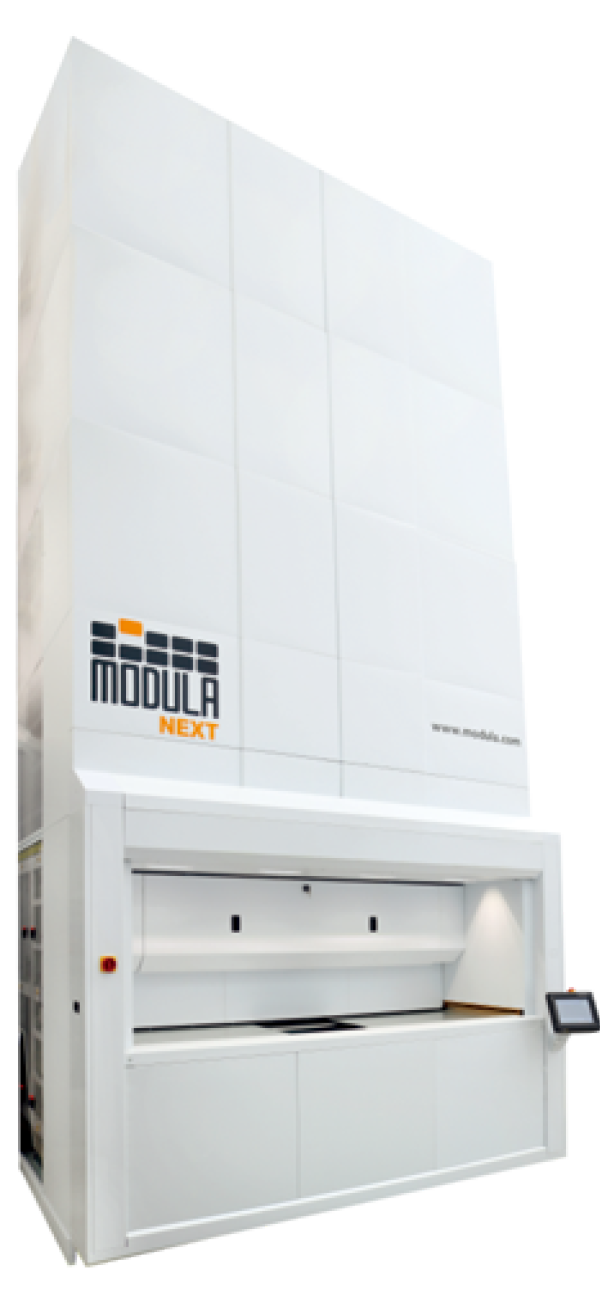

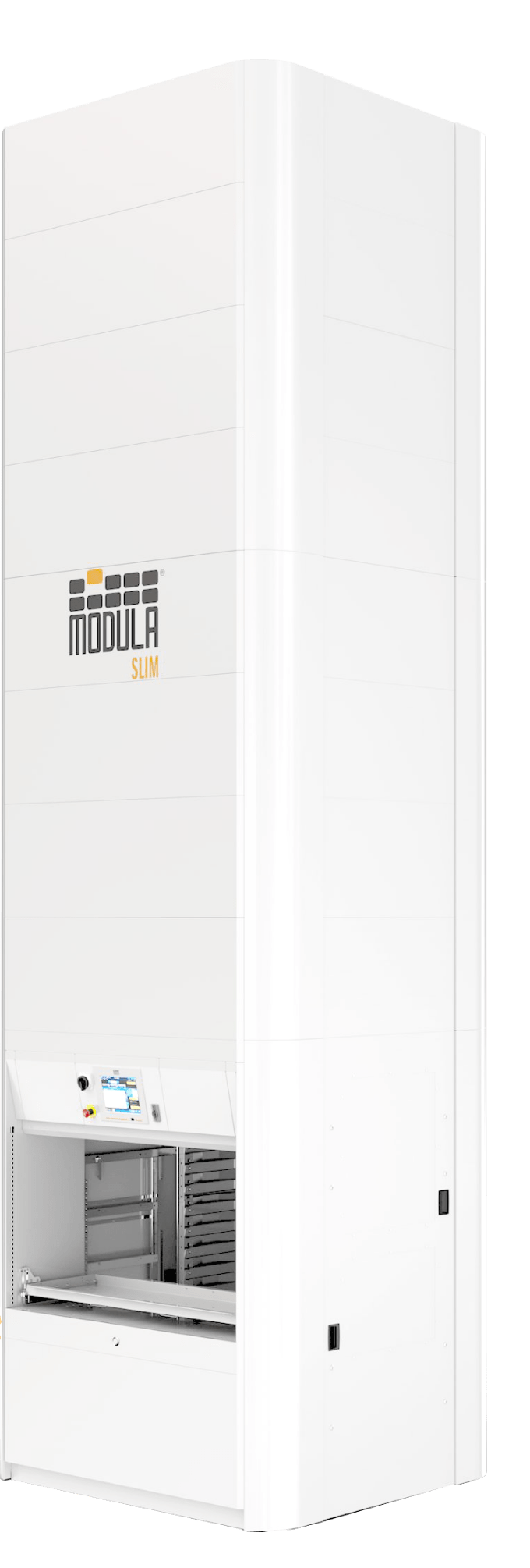
Vertical lift modules (VLMs) and vertical carousels (VCs) are both computer-controlled, automated storage and retrieval systems (ASRS) that occupy as little floor space as possible by taking advantage of the vertical height of a facility.
With both vertical storage solutions, companies can increase warehouse productivity significantly, by eliminating unnecessary walking, hunting, and climbing.
Although both deliver dense inventory storage in manufacturing and warehousing applications, these storage systems function in different ways.
A vertical carousel storage system stores parts on trays or carriers affixed to a chain that rotates, similar to a Ferris wheel.
On the other hand, the vertical lift module moves trays independently, with an extractor in the center, more like a vending machine.
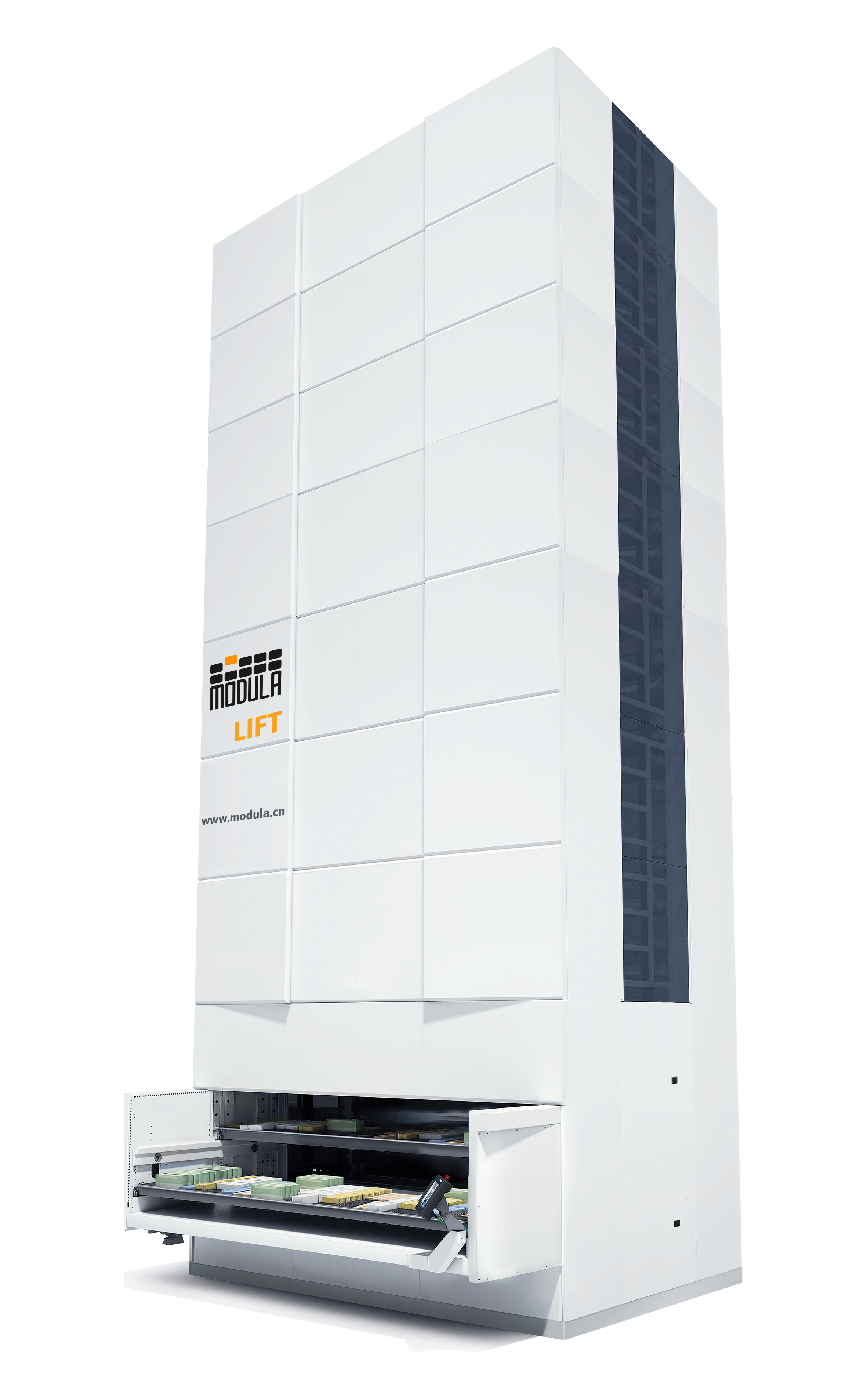
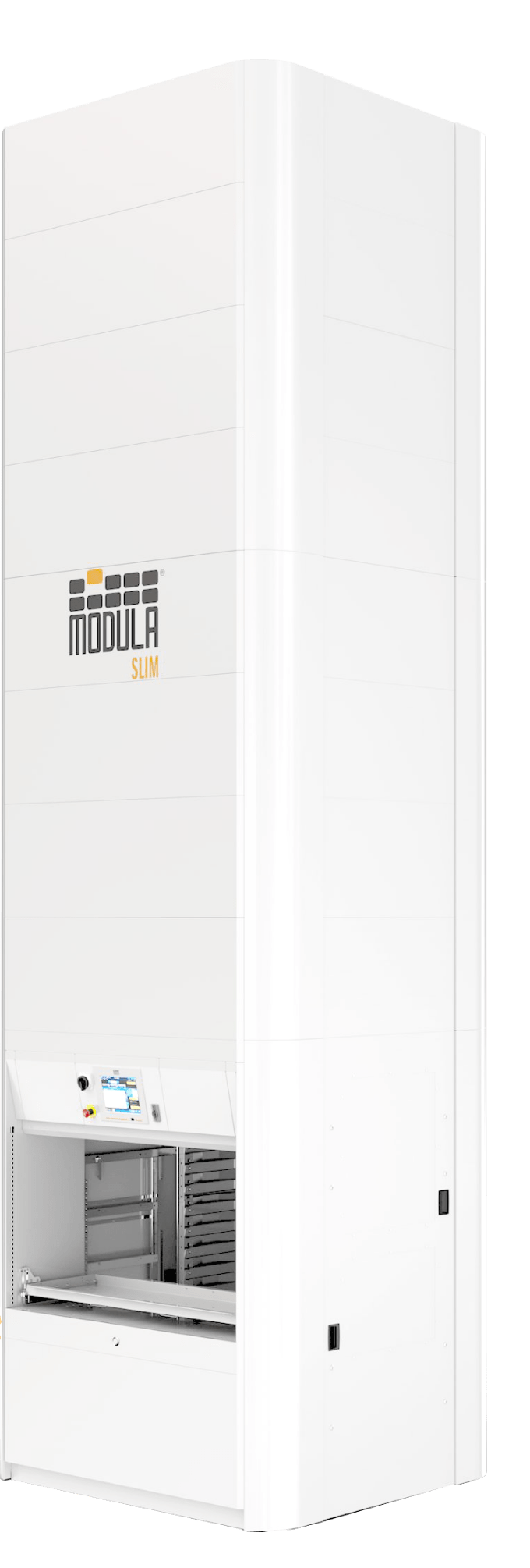
In the past, the only vertical storage product offered in the market was the carousel storage system.
Due primarily to the lack of flexibility and limited configurations, the vertical carousels were misapplied or configured incorrectly in many applications.
The introduction of the vertical lift module about 35 years ago started to change the face of vertical storage.
Thanks to the numerous configurations and advanced technology, the vertical lift module (VLM) offers a very flexible and scalable solution allowing for operations to change or grow, with easy implementations. Customers no longer need to worry about making the right decisions today that may not work in the future. Because of their easy configurability and scalability, VLMs can grow with companies as business strategies develop with emerging market trends and technologies.
9 Disadvantages Of The Vertical Carousel
The vertical carousel (VC), also described as a storage carousel or vertical rotating shelf system, has many disadvantages when compared to the VLM.
1. Limited Depth of the vertical carousel storage system
The vertical carousels come in different sizes in terms of width and height. However, when it comes to depth, a vertical carousel only offers 1.5m at the most.
- On the contrary, a vertical lift module can go more than two times deeper than carousel storage, offering a much better inventory space.
For applications with limited space, there are VLMs in the market capable of offering all of the benefits of the vertical lift module in the same footprint as a vertical storage system, such as the Modula Slim. One of the most compact VLMs on the market, Modula Slim has almost twice the load capacity (25,000 kg )of typical vertical carousels , without unbalancing issues.
2. Imbalanced Load Restrictions of Carousel Storage
A vertical carousel consists of shelves or carriers connected in a loop that rotates vertically and delivers stored goods to the operator. The movement is similar to a Ferris wheel. As the carriers are connected in a fixed order, the entire carousel system rotates every time the user needs to pick or replenish an item, causing many imbalance problems.
To avoid load imbalances, stored Items should have identical weights and similar sizes to optimize the storage space since the tray positions can’t be changed.
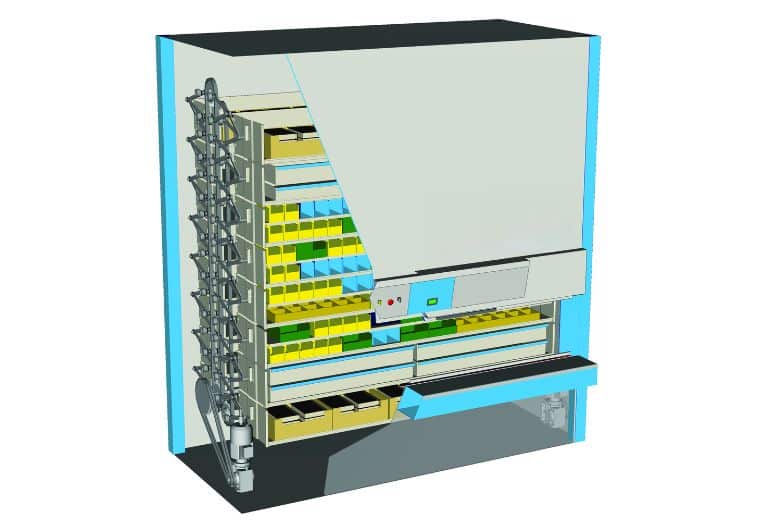
Vertical carousels may also limited in height, due to the above-mentioned balance issues.
These restrictions range in weight based on the model. With units of any substantial height and light duty, the rating could easily have imbalanced conditions due to a few carriers in a row being empty. This condition, over time, creates a lot of stress on critical components in the unit, requiring regular maintenance or causing premature failure of critical wear items.
If the unit reaches an imbalanced state, the motor can overload, and the carousel could shut down completely until the condition is corrected. The motor would struggle to get the carriers through the curve of the unit. A carousel with an odd number of carriers will experience these issues even more.
- There are no load imbalance issues with the VLM.
Vertical lift modules are composed of two tray towers — one in front and one in the back — along with a central elevator. Once the user calls the item, the elevator extracts and presents only the tray with the needed item, quickly, efficiently, and at an ergonomic height for the operator.
The trays are built to accommodate heavy loads (up to 990kg per tray) without strain or imbalance issues.
Vertical lift modules can reach up to 16m or more and contain trays of different heights, so waste storage isn’t an issue. For example, small items can be stored in one tray, while larger items can be stored in another tray.
The modular design of the VLM ensures almost unlimited flexibility. The height can be modified and adjusted to optimize the unit for the ceiling height by adding or removing modules. If you change locations or move to a different site, the VLM can be quickly adapted to the new height requirements.
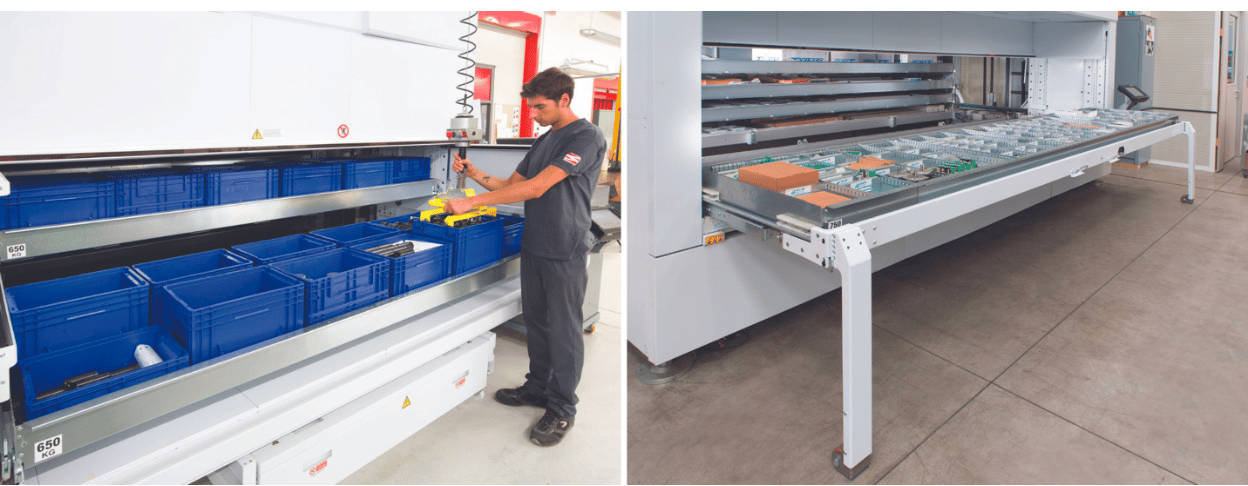
A vertical lift module can be easily integrated with lift-assist equipment and can be configured with a tray removal cart
3. Fixed Height Restrictions (pitch)
Again, because the carousel storage system is a closed-loop system with all carriers being tied together, there is no possibility of varying heights above the max height chosen at the beginning of the process. This is called the pitch of the carrier.
A carousel with a 12 pitch has a clear height of approx. 27cm. This means that the tallest product that can ever be put into the system is 27cm. You can add additional shelf levels to divide the 27cm up into smaller levels, but you can never go taller. This would require a new unit. For this reason, there is no room for error when designing the system and no flexibility for future product or process changes.
- The VLM offers dynamic storage locations and flexible configurations. The VLM has dynamic storage locations that change on –the fly with the size of the product being placed into the tray. These heights can range has no limitation.
- Vertical lift modules can easily accommodate items of different sizes and weights. Trays can be organized for every type and size of stored item. Thanks to partitions and dividers, companies can create the exact number of storage locations required, and their configurations can be adjusted at any time to accommodate changes in the size or quantity of stored items or seasonal demands.
A height-detection system determines the vertical dimensions of items as the tray is put away, calculating adjustments in real-time to maximize storage density within the unit.
The VLM has dynamic storage locations that change on the fly with the size of the product being placed into the tray
4. Product Movement in the Carousel Storage System
Due to the carousel’s rotating retrieval method and the fixed locations, every carrier is traveling in order to get the required product to the access window. This means that all products are also traveling during every transaction. This may not be desired for some products, as it may be fragile or sensitive to continuous movement.
- The VLM only moves the necessary tray, one at a time, to the access window in order to retrieve the required parts. This eliminates unnecessary product movement and reduces the risk of shock to the product.
5. Front Picking Restriction
Because the Vertical carousel storage system is a closed loop system and there is always another carrier directly above it, the product must be picked from the front, not the top. This means that you must reach into the face of the carrier to pick up parts.
This restricts not only the visibility of the products but also the number of products users have access to at any given time. Top picking in a carousel is only possible using totes or boxes that can be pulled out of the carrier, exposing the entire product. This adds unnecessary steps to the picking process.
- The VLM always provides top picking, making all products easy to see and access. There are no additional movements added to the pick cycle. The selected tray is brought into the working opening, where it is 100% visible and accessible to the operators.
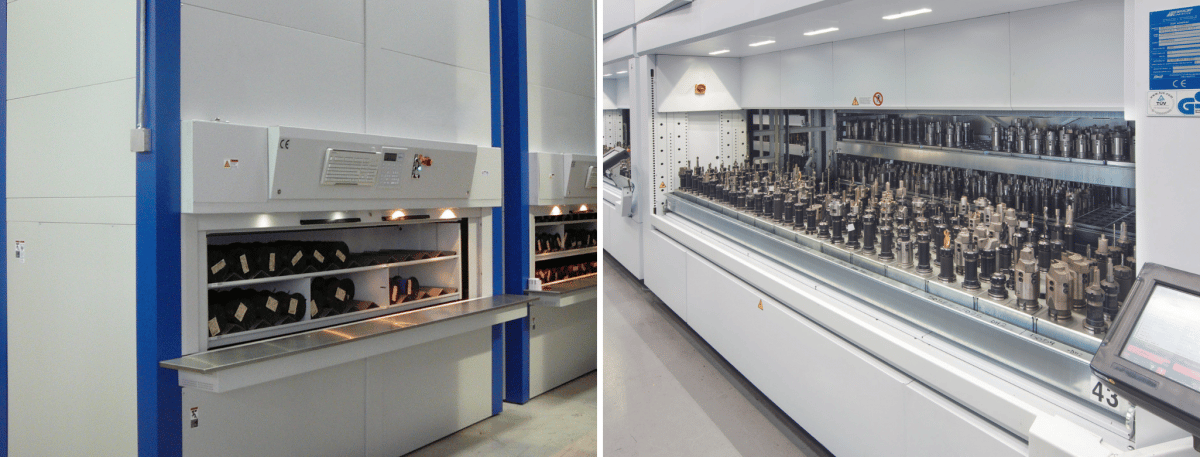
Front picking: Vertical Carousel vs Vertical Lift Module
6. Security Issues with Vertical Carousel System
The vertical carousel rotates all carriers past the access window in order to get to the required storage location. This makes all products accessible, even in cases where security is required, or product tracking is important. Any carrier can be stopped at the access window along the way, making it easy to pick the wrong part or a part they like.
- Because the VLM only delivers one tray at a time, the other products are kept secure in the unit. Only the desired product is brought to the access window, making it possible to restrict access to other products when and if necessary. The vertical lift module can also be equipped with several safety options, such as budget EKS or RFID readers. Thanks to the automatic closing door, the materials stored are kept inaccessible when the machine is off or unattended.
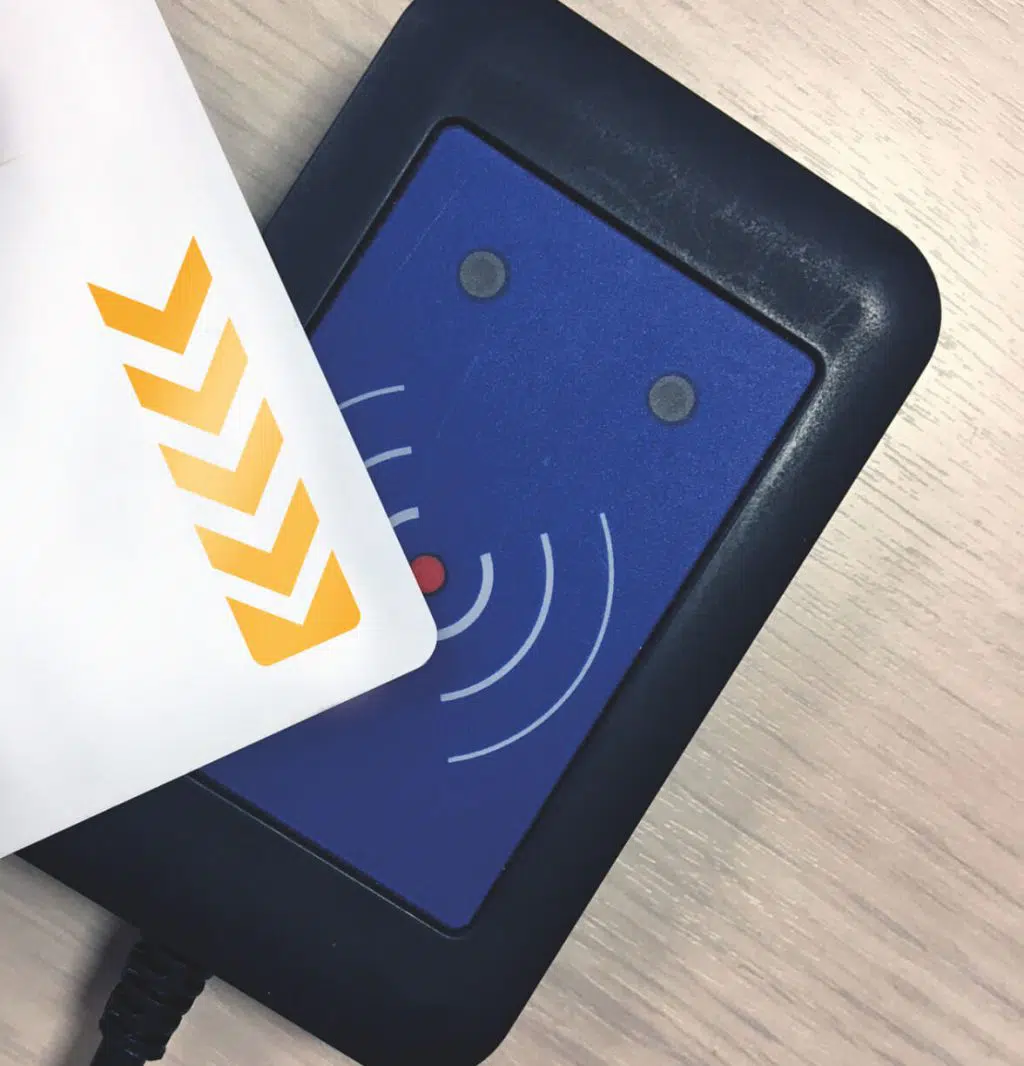
EKS or RFID readers
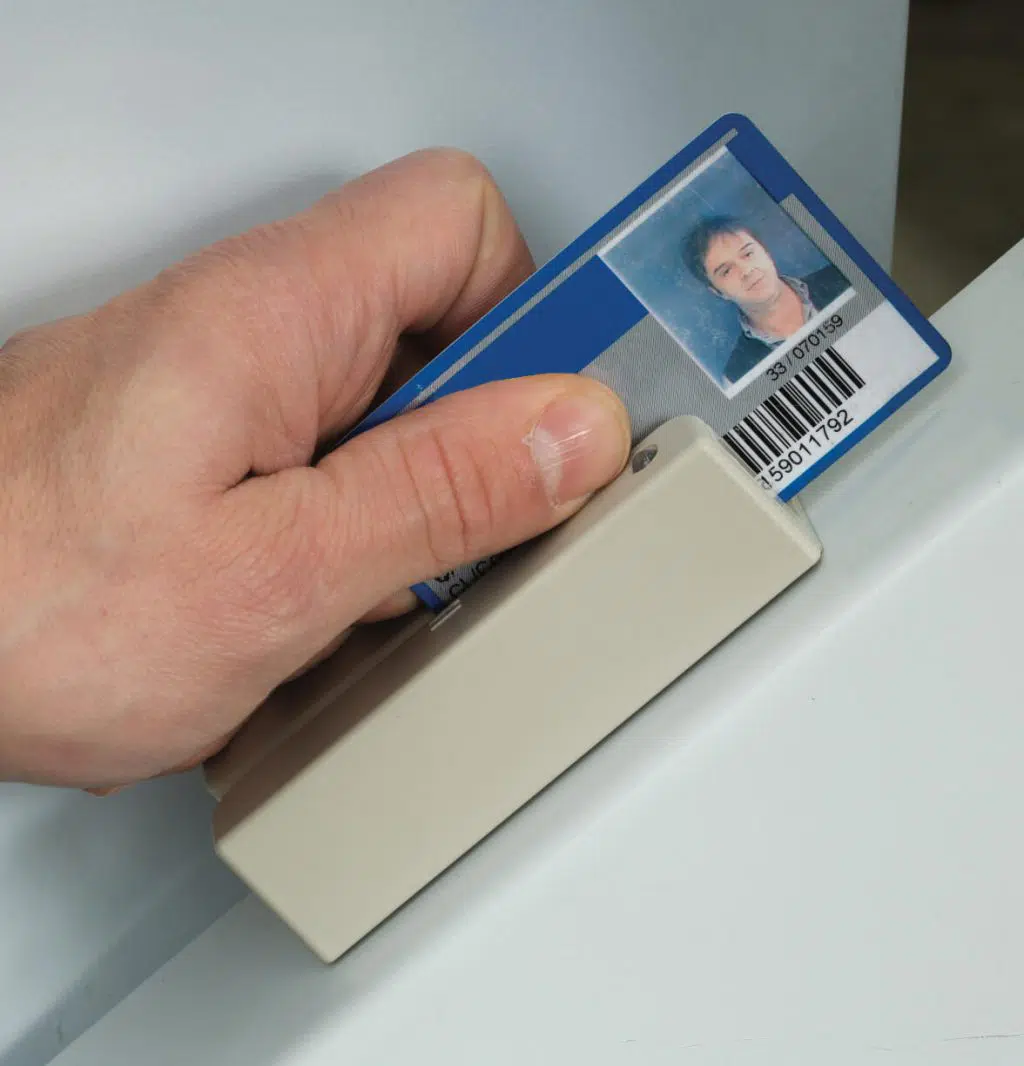
Badge readers
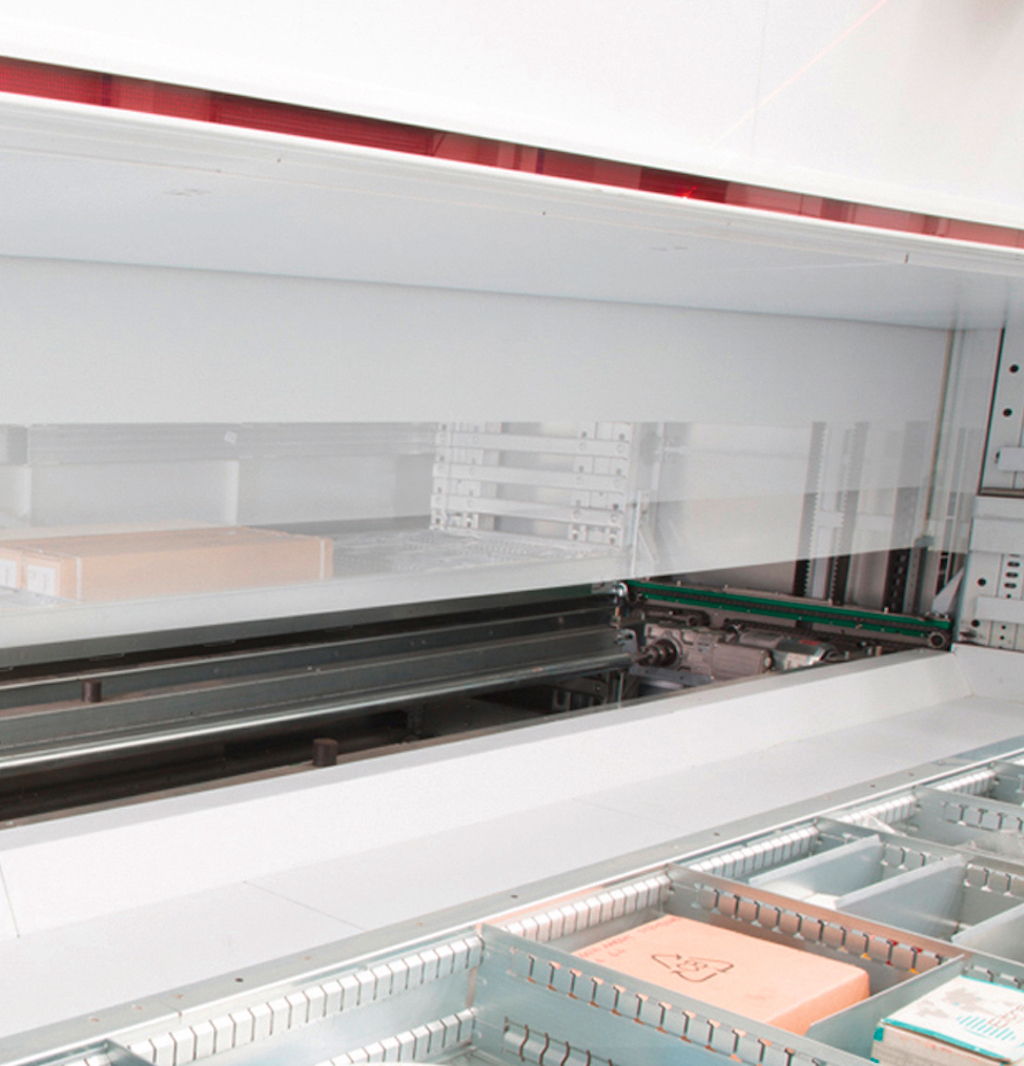
Automatic Closing door
7. Dual Access
Dual access functionality for a vertical carousel is much different than with the vertical lift module. Because the VC system of carriers is tied together in one tray, it is not possible to work at two access openings at one time. Each access needs to be given (or take) priority over the other.
Again, this is because if one carrier moves, they all move. Also, it is not possible to get various combinations of carriers to appear at each corresponding access opening at any given time. Some systems even require that the door of the opposite opening be closed in order for the other opening to work. If this is true, and they do not close the door, the other side is not functional.
- The VLM has the ability to work from both access openings simultaneously. This means that after the lift has delivered a tray to one access, it can continue on to deliver (or remove) one from the other opening. The workers are free to work on their respective trays at any time while they are in the access opening. This creates a more productive environment for both picking and replenishment, as all replenishment can occur during the picking cycle.
- The vertical lift module can also extend over different floors, with access openings on the front and rear, allowing operations on multiple levels simultaneously. The units can also be installed outside of the building to further expand storage space.
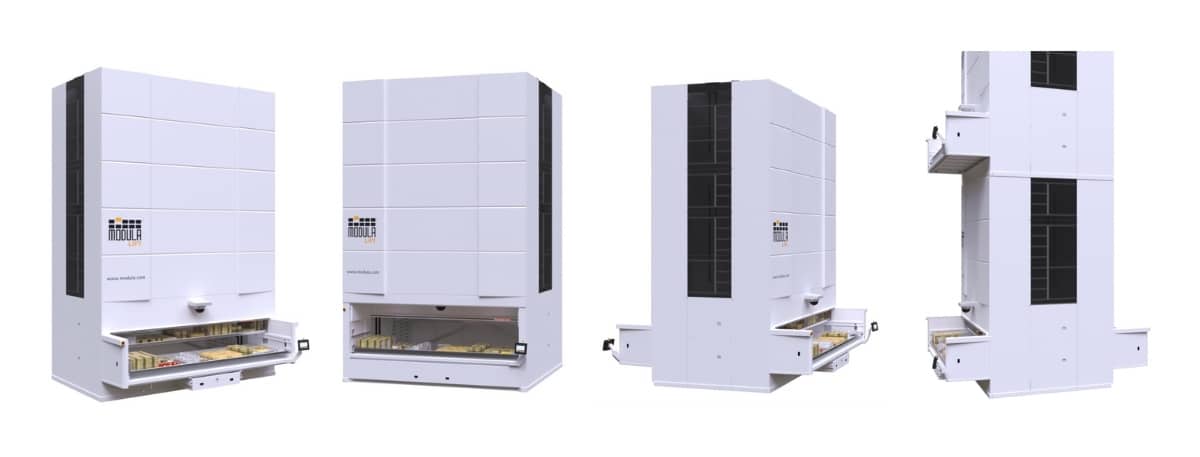
Vertical Lift Modules -Internal and external bay, opposite bays, bays on different floors
8. Less Efficiency and Speed in Picking with the carousel storage system
Both in picking and replenishment operations, vertical carousels tend to be slower and less efficient.
When users need to pick an item, they need to wait for the entire set of carriers to move before accessing the needed part.
During loading operations, due to the unbalancing issues, items and carts need to be loaded with careful consideration. Once items are placed into a carrier, the carousel needs to rotate 180 degrees, to ensure that the loads are evenly distributed.
Due to its retrieval methods, the picking speed and efficiency of a VC are quite limited.
- Vertical lift modules can save you time in picking items since you don’t need to wait for the entire set of trays to move – just the tray holding the item or goods.
In addition, the machine can be equipped with a dual delivery bay to further enhance the picking speed. While the operator is working one tray, the elevator is retrieving and staging the second tray in the queue, decreasing waiting time and speeding up the picking process.
Finally, With the greater range of visual aids that they can provide (for example, laser pointers to indicate where the needed item is located), vertical lift modules provide faster and more accurate retrieval for your operators. At Modula, our Modula Lift Modules offer picking speeds of 300 lines per hour or more.
9. Installation process and time
One of the major problems with vertical storage carousels is getting the carousel into the facility, as they are installed as one unit and can’t be installed in sections.
A VC will usually take up to four days for installation.
- Vertical lift modules come in separate pieces that can be easily transported, making it possible to install a VLM in only two days. The repair processing also tends to be faster with VLMs, due to the most advanced technology these units are built on.
What Is the ROI for Vertical Carousels Storage system and Vertical Lift Modules?
The price of a new vertical carousel storage system and a vertical lift module is roughly the same.
But considering the previously mentioned disadvantages that come with a vertical carousel, you’ll see a quicker ROI with vertical lift modules.
Wrapping up on Vertical Carousels and Vertical Lift Modules
Vertical carousels may have been around longer than vertical lift modules, but the advantages you can reap from VLMs are clear. If you are considering an automated storage and retrieval system, it is important to evaluate which system is right for your handling and picking needs.
At Modula, we offer two vertical lift modules:
- Modula Lift: Considered our most popular vertical lift module, Modula Lift is available in a wide array of capacities and sizes, used by businesses to modernize operations.
- Modula Slim: This vertical lift module is designed to fit small spaces with similar functionalities as the Modula Lift.
The advantages of a vertical lift module include:
- Minimal footprint, saving valuable square footage while maximizing storage potential
- High throughput rates
- High inventory accuracy to eliminate miss-picks and errors during put away and replenishment.
- Increased security while providing clean storage for your products
- Modular design for future adaptability
- Ergonomic pick height for all products
- Ability to train workers in a significantly brief period
Ready To Start Your Automation Journey?
From analysis to design to implementation, Modula helps you achieve your operation’s goals to boost your competitive edge. Let us show you how you can:
- Increase throughput
- Lower cost per order
- Eliminate residuals completely
- Reduce footprint size
- Increase capacity
- Improve order accuracy
- Dramatically increase efficiency
- Reduce labor requirements