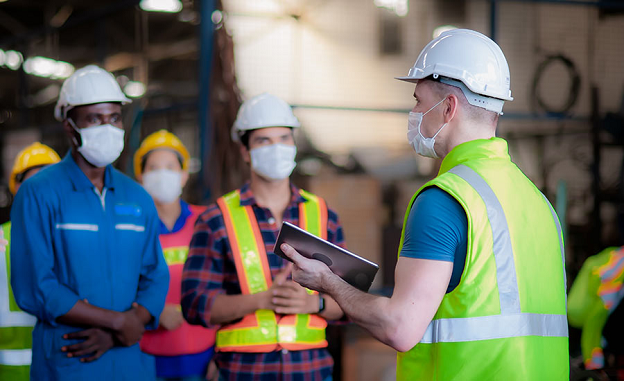
In the last ten years, Australian workplaces have seen over 1,850 fatalities due to traumatic injuries, highlighting warehouses as some of the most hazardous environments.
Like manufacturing facilities and chemical plants, warehouses require rigorous safety measure enforcement.
So, how can you ensure employee safety as they move between inventory shelves and picking stations daily?
We’ll cover the top warehouse safety guidelines and tips for keeping your warehouse operators safe and productive.
Plus, we’ll introduce you to leading warehouse safety solutions at Modula APAC to streamline operations and enhance safety protocols, ensuring a safer and more efficient workplace for everyone.
What Is Warehouse Safety?
Warehouse safety is a set of guidelines and proven industry methods that help warehouse employees promote safe workplace practices.
Common safe workplace practices for warehouses include wearing protective gear, adhering to proper lifting techniques, keeping aisles obstacle-free and ensuring equipment is well-maintained.
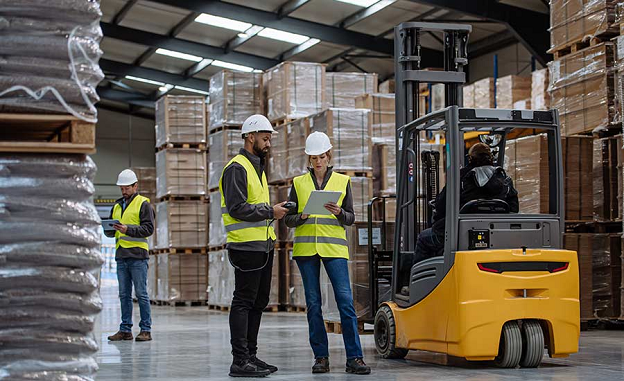
Key Benefits of Practicing Warehouse Safety
Integrating warehouse safety into your operations provides several key benefits that protect employees and enhance overall business performance.
1.Prevents Injuries and Potential Accidents
Warehouses can be hazardous environments, posing risks of falls, machinery accidents and overexertion injuries.
When you implement safety measures like proper training and regular equipment inspections, you can help your warehouse staff reduce the likelihood of accidents.
2.Improves Productivity and Morale
A safe workplace is an efficient one, as fewer accidents lead to reduced downtime and disruption, resulting in increased productivity and smoother operations.
Warehouse staff are also more likely to be engaged and committed when they feel their safety is a priority.
3.Enables Your Employees To Meet Compliance Obligations
Warehouses are subject to various health and safety regulations, such as Occupational Health and Safety (OHS) in Australia.
OHS Australia standards mandate a wide range of protective measures to ensure a safe working environment.
These measures include regular equipment maintenance to prevent mechanical failures and the use of personal protective equipment (PPE), among others.
Common Hazards in the Warehouse
From overexertion to equipment-related accidents, the most common warehouse hazards include:
- Slips, Trips, and Falls:Wet floors, uneven surfaces and cluttered walkways can cause falls, one of the most common types of workplace injuries.
- Collisions or Impact-Related Accidents:Unexpected programme changes, component malfunctions, and erratic movements can lead to collisions between robots and warehouse staff.
- Forklift Accidents:Improper forklift operation can lead to collisions or overturns that may result in serious injuries or even fatalities.
- Struck-by or Caught-in/Between Machinery:Moving parts or machinery can strike or catch workers, which can result in serious injuries.
- Manual Handling and Lifting:Incorrectly handling or lifting heavy objects can cause strains, sprains and musculoskeletal injuries.
- Falling Objects:Improperly stored items may fall and injure warehouse employees.
- Hazardous Materials:Incorrect handling or storage of chemicals and other hazardous substances can lead to health problems, such as skin irritations.
- Fire Hazards:Improper storage of flammable materials or inadequate electrical safety measures can increase the risk of fires.
- Poor Ergonomics:Repetitive tasks and poorly designed workstations can cause chronic injuries. such as carpal tunnel syndrome or back problems.
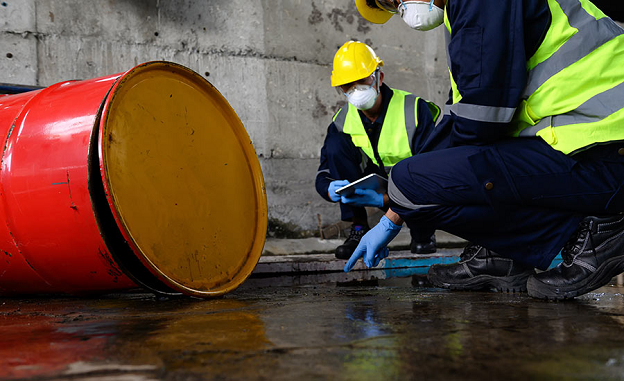
Is Automated Handling a Hazard?
Yes, automated handling can pose hazards in warehouses if not properly managed.
While designed to boost efficiency and minimise human error, warehouse technologies like robotic equipment and conveyor belts pose some risks that include:
- Mechanical Failures:Automated equipment may malfunction without regular maintenance. For example, a conveyor belt could misalign during operations, potentially damaging goods or injuring nearby workers.
- Human Errors:Human errors, such as incorrect data entry and inadequate training, can cause programming issues that lead to unexpected robot movements or actions. However, OSHA identifies the main issue as familiarity with the robot’s repetitive motions, causing potential operator complacency and reduced alertness to potential hazards.
- System Errors:Software glitches or programming errors can cause unexpected behavior from automated systems, potentially harming nearby employees.
- Obstruction Issues:Cluttered inventory on walkways where automated equipment passes can cause jams or malfunctions, potentially leading to accidents or damage.
- Power System Failures:Power sources, whether hydraulic or electrical, can interfere with control system signals or power-supply lines. Electrical overloads increase the risk of fires and workers may experience electrical shock hazards with the release of stored energy.
- Improper Installation:Flawed installation may create different hazards over time, such as increased wear and tear on parts and operational failures that might endanger employee safety.
While automation presents various safety challenges, they remain a core component to enhanced operations.
Automated warehouse solutions optimise processes, diminishes physical strain on workers and can significantly boost productivity and inventory accuracy.
Effective training, consistent upkeep and clear safety protocols are paramount in mitigating these risks and ensuring safety with automated handling systems.
Warehouse Safety Best Practices
Implementing best practices in warehouse safety is crucial for employee protection, boosting productivity and industry standard regulation compliance. Here are 10 warehouse safety best practices you can implement in your workplace.
1.Regular Safety Training
Conduct monthly safety training sessions covering topics such as proper lifting techniques, correct machinery usage and emergency response procedures.
2.Proper Use of Personal Protective Equipment (PPE)
Make wearing PPE, including steel-toe boots, high-visibility vests, and hard hats on the production line a company policy.
Monitor your employees to ensure compliance and that the equipment is in good condition.
3.Forklift Safety
Only allow certified employees to operate forklifts and ensure they receive annual refresher training. Implement a daily checklist for operators to inspect their forklifts before use, focusing on brakes, steering and warning devices.
4.Effective Signage and Floor Markings
Use clear, visible signs to mark pedestrian walkways, forklift lanes, and hazardous areas. Apply and regularly maintain floor markings to keep these areas well-defined and visible.
5.Routine Equipment Maintenance
Establish a maintenance schedule for all warehouse equipment, such as conveyors, lifting devices, and storage racks.
Maintain detailed records of maintenance activities and address potential issues to prevent equipment failure.
6.Safe Storage Practices
Ensure that heavy items are stored on lower shelves to reduce the risk of falling objects.
Regularly inspect stacking and storage techniques to guarantee they meet safety standards and adjust as necessary.
7.Emergency Preparedness
Conduct regular fire drills and ensure all employees are familiar with emergency exit locations and fire extinguishers. Always keep evacuation routes clearly marked and obstruction-free.
8.Hazardous Materials Management
Train employees in properly handling and storing hazardous materials, such as batteries and radioactive materials.
For example, keep areas well-ventilated and ensure that all containers are clearly labeled and securely closed. Additionally, ask your employees to store hazardous inventory separately to prevent any chemical reactions or spills.
9.Ergonomics in the Workplace
Provide adjustable workstations suiting various heights and body sizes to minimise the risk of musculoskeletal injuries. Offer ergonomic training to help employees optimise their workspaces.
10.Traffic Management
Implement a traffic management plan to regulate the movement of vehicles and pedestrians.
For example, you can install lanes marked specifically for different types of vehicles, such as forklifts and delivery trucks, as well as separate paths for pedestrians.
Use physical barriers to enforce these lanes and implement one-way traffic systems to prevent collisions.
Warehouse Safety Solutions at Modula APAC
At Modula APAC, we provide scalable solutions that are built to promote an ergonomic and safe workplace by removing the need to climb the stairs or reach high and low areas.
For instance, Modula SLIM is ideal for environments with limited floor space that require flexible vertical storage. They keep your employees safe by occupying less space, further improving accessibility and organization.
Additionally, these solutions deliver products to a picking bay set at an ergonomic height, making it easy and safe for your employees to operate.
But what happens if your facility catches fire? The Modula LIFT is here to help.
The Modula LIFT is the ideal automated warehouse solution for all types of products, components, and spare parts, across any environment or sector. It is equipped with the Modula Firefighting System.
All fire extinguishing methods depend on disrupting the “fire tetrahedron,” the four factors that combine to start and sustain a fire.
The Modula Firefighting System transcends traditional methods by using a non-toxic extinguishing agent composed of ultra-fine solid particles, each smaller than 10 micrometers in diameter.
This agent stays airborne longer and leaves significantly less residue than traditional methods, making it a superior choice for fire safety.
Ready to prioritise safety? Feel free to reach out and see how we can customise our technology just for you.