Hello everyone, I’m Liu Dunhou, Sales Director of Modula China. Today, I’d like to talk to you about our newly launched automated storage equipment — Flexibox.
This product is a brand-new solution meticulously developed by Modula specifically for the crucial “picking” process. We’ve given it a strong positioning statement — “Pick the Best”, aimed at redefining the standards of smart warehousing through more efficient and precise picking capabilities.
It’s not just a slogan — it’s Modula’s redefinition of efficiency, accuracy, and space utilization.
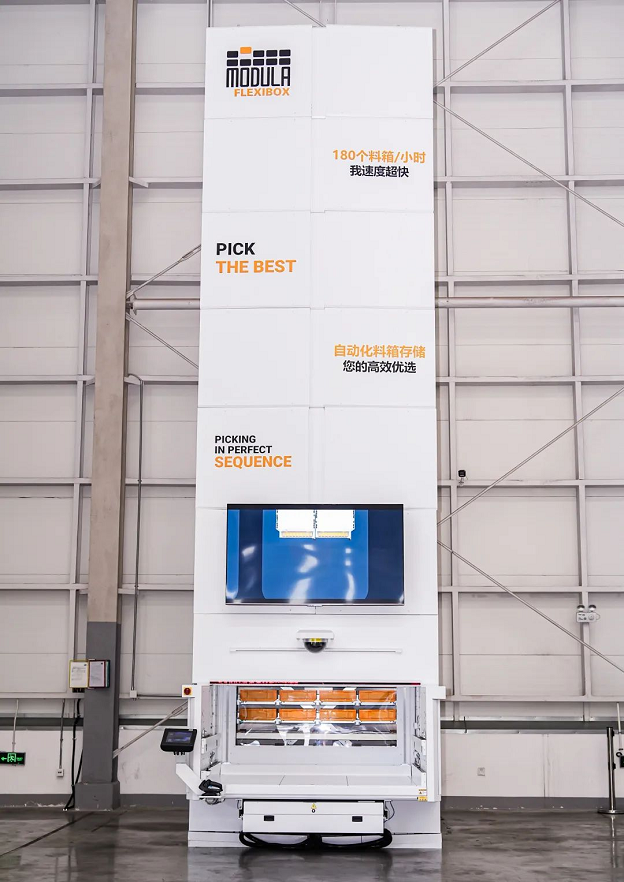
01 Why Launch the New Product Flexibox?
In today’s landscape of high-frequency operations and increasingly fragmented orders, the efficiency bottleneck in the picking process is becoming a common concern for more and more enterprises.
The challenges are particularly evident in the following scenarios:
- A single order involves multiple SKUs, requiring frequent bin switching and repeatedly interrupting the picking workflow.
- Bins are scattered, and operators spend large amounts of time waiting and searching.
- During peak operational hours, manpower struggles to keep pace with the order rhythm, limiting overall efficiency.
Flexibox was born precisely to address these pain points. It does not replace existing products but rather serves as a “high-efficiency picking specialist” within our family of solutions — designed to solve the often-overlooked small issues that, in fact, significantly impact overall warehouse efficiency.
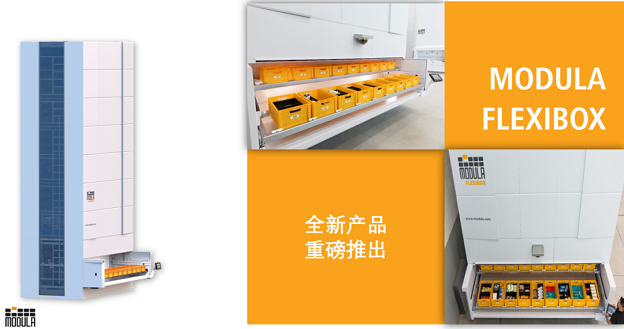
02 How Does Flexibox Improve Picking Speed?
Its core concept is simple: prepare multiple bins at the same time and complete multiple picking actions in one go.
For example, when picking 9 materials, traditional equipment might present one tray at a time, requiring up to nine back-and-forth cycles for a single order.
Flexibox, however, can deliver all nine required bins to the access opening at once, allowing the operator to stay in place and pick by light indicators, completing tasks efficiently.
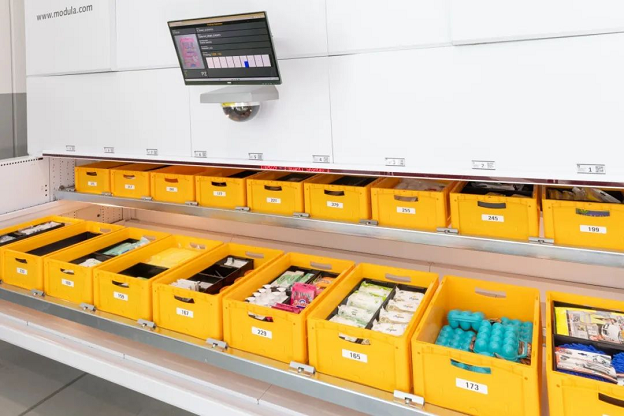
We’ve designed a dual-tray system — while one side is picking, the other is preparing the next round of materials. No matter how busy the task, there is never idle waiting.
There is also a very “smart” companion — the shuttle fork. While the lift moves up and down, this horizontally moving fork accurately pulls the designated bin from its storage location and places it onto the service tray.
03 Picking + Sorting = Fully Automated
The charm of Flexibox lies not only in fast picking, but also in its integration with a sorting system (Put Wall), which together almost form a “mini sorting center.”
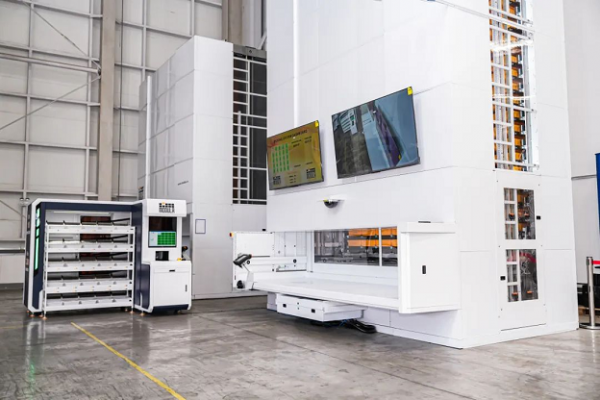
Operators simply follow the light indicators to retrieve materials and place them into the corresponding order bins. The system automatically records the order fulfillment progress. For instance, if 10 items need to be picked, each pick updates the progress by 10% — until reaching 100%. Once the light is on and the box is full, the task is complete, and the operator can move on.
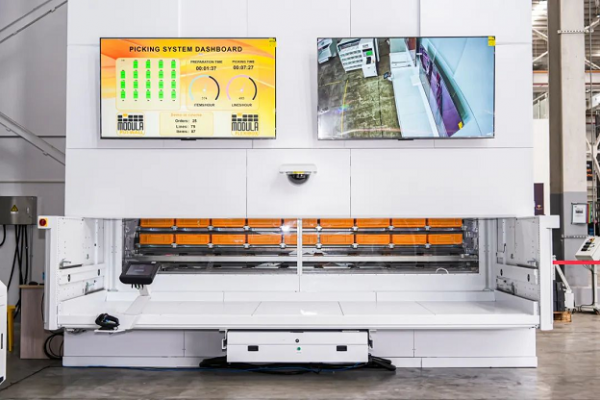
The entire process is not only fast but also clear, visualized, and error-free.
04 How Efficient Is It?
If you’re interested in the numbers, here are some key indicators:
- Single picking efficiency: up to 180 bins/hour
- Batch picking: up to 360 bins/hour
- Idle-time batch combination: peak efficiency over 500 bins/hour
These figures are not from laboratory tests, but from real-world operations. If you’ve ever lost time waiting for trays, you’ll understand just how significant this efficiency gap is.
05 Multiple Models, Flexible Compatibility
Flexibox uses standard 400×600 mm bins, with each tray capable of carrying up to 9 bins. Combined with three sets of access openings, the entire system can support up to 6 service trays operating simultaneously. The maximum machine height reaches 20 meters, easily accommodating thousands of bins.
Currently, five width models are available — 1.5 m, 1.9 m, 2.5 m, 3.1 m, and 4.1 m — catering to a variety of scenarios from small-batch picking to large-scale sorting.
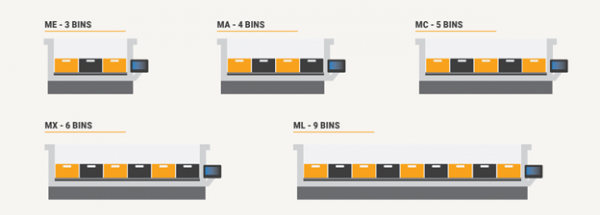
Moreover, Flexibox is fully compatible with our mature Modula WMS system. Existing customers can seamlessly expand by simply adding new devices, without changing their software platform.
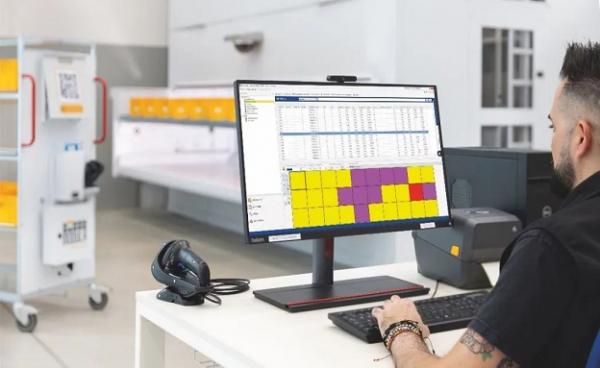
06 What Industries Is It Suitable For?
Flexibox is especially well-suited for the following scenarios:
- Multi-SKU, high frequency picking warehouses (e.g., 3PLs, e-commerce)
- Kit picking and order-based allocation (manufacturing, workstation prep)
- High-value product management (tools, precision components)
- Distributed order fulfillment centers
- Unmanned warehouses in collaboration with AMR/AGV robots
Its design intent is clear: make warehouses smarter, operations simpler, and workflows more compact.
Summary
The introduction of Flexibox is not a minor tweak — it’s a complete rethinking of how to achieve more efficient picking.
If you are looking for a solution that picks fast, picks accurately, can expand at any time, and integrates seamlessly with your existing systems, we invite you to visit Modula’s Suzhou factory to explore the real-world applications and picking efficiency of Flexibox, and obtain a customized automation picking optimization solution.