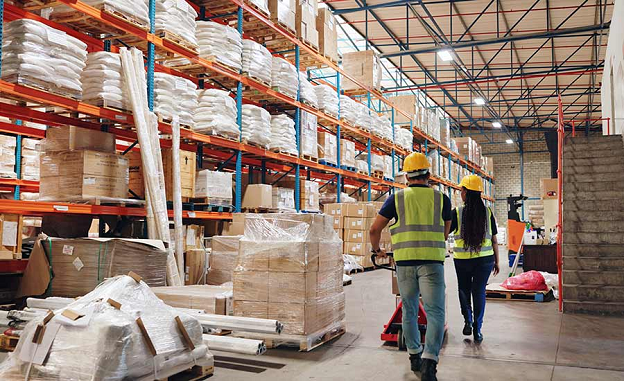
For E-Commerce business owners, order fulfilment is a crucial part of operations.
And, as your business grows, handling customer orders in-house may become impractical due to limited storage space or the need for faster shipping times — especially since two-thirds of shoppers around the world expect to receive their items within 24 hours.
If you’re thinking about implementing a 3PL provider to your operations, you’re most likely evaluating its advantages and disadvantages.
In this article, we’ll help you decide by explaining everything you need to know about 3PL.
We’ll define what it is, discuss the benefits of working with a 3PL partner and walk you through the top considerations when choosing a provider.
What Is 3PL?
Third-party logistics (3PL), also known as a 3PL partner, is the outsourcing of eCommerce logistics operations, such as transportation, warehousing, kitting, managing inventory, packaging and clearing customs to an external service provider.
Leveraging a 3PL provider offers plenty of benefits, from providing tech services and cost savings to boosting efficiency in a competitive market.
3PL vs. 4PL
A 3PL provider handles specific logistics services, such as storage, transportation and order fulfilment. They’re an external partner that manages the day-to-day logistics operations, but the client still maintains control over aspects of the supply chain.
On the other hand, 4PL providers (also known as lead logistics providers) take logistics outsourcing a step further by managing the client’s entire supply chain.
They act as the centralised point of contact for operational support and communication with other vendors, optimising logistics for merchants by handling their strategic operations.
A 4PL oversees relationships with various 3PL providers and manages transportation, inventory and warehouse technologies.
When collaborating with a 4PL partner, you don’t need to manage multiple vendor relationships or make general logistics-related decisions.
Another key difference between 3PLs and 4PLs:
3PL providers often own the assets they need for logistics services, such as warehouses and fleets. In contrast, 4PLs typically don’t own physical assets. Instead, they provide logistics expertise and IT systems, like fulfilment software.
The 3PL Order Fulfilment Process
The fulfilment process plays a key role in supply chain management, following several steps that align with standard supply chain procedures.
Whether you handle logistics internally or with the help of a 3PL or 4PL, these steps ensure the successful completion of an order.
1.Receiving
The first step in the order fulfilment process is receiving. Receiving is the process of accepting, unloading and storing inventory in a warehouse or fulfilment centre.
While all types of 3PLs follow this standard step, each may use a slightly different method to receive their inventory.
For example, some 3PLs may use automated systems to scan and sort inventory as it arrives, while others manually check and record items to ensure accuracy before storage.
2.Storage
Once products arrive at the fulfilment centre, employees organise and store them. Each SKU is assigned a designated location in the 3PL warehouse, tracked by a shelf, bin or pallet number.
3PLs vary in their storage capabilities, and not all have the same type or amount of storage.
The order fulfilment process heavily relies on warehousing, so it’s crucial to choose a 3PL that has enough space to support all your products and can scale with your growth.
3.Picking
When a customer places an order, your 3PL partner should quickly locate the item and prepare it for packing and shipment.
This requires the 3PL to maintain accurate inventory records and efficiently process customer orders to speed up delivery.
4.Packing
Different products have specific packing needs for safe transportation, and your 3PL should be equipped to handle these requirements.
Common packing materials include paper, tape, bubble mailers, dunnage and boxes. With their industry expertise, 3PLs can determine the best packing methods to ensure your products are securely shipped out.
5.Shipping
Your 3PL partner manages shipping your goods to customers and may work with different carriers.
Some may choose the least expensive option, while others prefer specific carrier partners. Before partnering with a 3PL, understand their shipping processes and transportation services.
Additionally, consider how they handle shipping labels. Some 3PLs print and purchase labels for you, while others pass this cost on to you.
6.Returns
Most 3PLs offer returns processing services for customers who aren’t happy with their orders, such as damaged products. They’ll process the returned goods and either restock the item in your inventory or get rid of it, depending on your policy.
Who Needs a 3PL Warehouse and Partner?
Whether you run a startup or have a multinational corporation, a 3PL warehouse and partner can optimise your resources and increase efficiency.
Consider a 3PL partner if you:
- Have limited warehouse space
- Struggle to manage a growing customer base
- Face an increasing number of customer complaints
- Encounter delays in your fulfilment process
- Experience labor shortages
- Make operational changes, such as switching from local to international manufacturers
Key Benefits of Collaborating With 3PL Partners
When you leave it to the experts, you can focus on your core competencies and allocate resources more effectively.
- Increased efficiency:3PLs streamline logistics operations, from warehousing to transportation, streamlining the entire supply chain.
- Cost savings:Partnering with a 3PL can reduce operational costs by eliminating the need for in-house logistics infrastructure and personnel. For example, instead of moving to a larger warehouse, your business can use a 3PL’s existing facilities and resources, helping you further save on property investment and management expenses.
- Scalability and flexibility:3PLs can easily adjust to fluctuating demand and scaling operations, accommodating business growth without the need for additional investments, such as
- Leverage the 3PL’s experience:3PLs understand the industry like the back of their hand. Use their specialised knowledge and experience to improve logistics strategies and operations. For example, 3PLs can provide insights into the most efficient routing and shipping methods or suggest the latest technology to streamline inventory management and order fulfilment processes.
How To Find the Best 3PL Partner
Taking the time to research and carefully evaluate potential partners can pay off by providing a more streamlined supply chain, increased revenue, and happier customers.
1.Research
Begin your search by gathering information on different 3PL providers. Look at reviews, case studies and testimonials to gauge their reliability and performance.
Ultimately, when choosing a 3PL partner, ensure they offer the following:
- Experience with companies in your industry
- Competitive pricing
- A solid reputation
- Scalability to grow with your business
- Advanced technology, including automated solutions for warehouse management and order fulfilment
- The flexibility to quickly adapt during seasonal demands, such as Black Fridays or holidays
2.Evaluate the Partner
Assess potential partners based on their experience, capacity, and alignment with your business goals. Consider their customer service, scalability and flexibility in handling logistics challenges.
You can also ask if they:
- Operate an automated warehouse
- Provide modular and scalable solutions
- Take advantage of picking solutionsand a warehouse management system (WMS)
3.Make Sure the 3PL Provider Is Using Modula’s Automated Solutions
To determine if a 3PL provider can boost your operations, ask if they use Modula APAC’s automated solutions.
At Modula APAC, we equip 3PL providers with state-of-the-art warehouse technology, such as WMS software, vertical lift modules, such as our Modula LIFT NG, Modula NEXT, Modula SLIM horizontal carousels and automated picking systems to maximise storage, strengthen productivity and minimise human error.
Our solutions enable 3PL providers to:
- Safely store and organise SKUs
- Comply with regulations for storing sensitive items like chemicals, electronics, pharmaceuticalsor food, using special applications, such as Climate Control and Clean Room
- Reduce human workforce dependency, thereby further decreasing human error
- Cut costs through enhanced efficiency and productivity