Warehouse space is becoming increasingly limited, prompting managers to consider moving to larger and more expensive to accommodate growing operations.
However, despite rising warehouse expenses, there are efficient methods available to enhance operational efficiency within your current space.
We’ll discuss vertical lift modules (VLMs), their advantages, and how they outperform vertical carousels.
We’ll also demonstrate how our vertical lift modules can revamp your warehouse operations and significantly boost profitability.
What Are Vertical Lift Modules (VLMs)?
A vertical lift module (VLM) is a type of automated storage and retrieval system (ASRS) that operates on the goods-to-person principle.
VLMs maximise storage by effectively utilising the ceiling height, making it a great option for smaller facilities.
Vertical Carousels (VCs) vs. Vertical Lift Modules (VLMs): Which Is Better?
Right off the bat, vertical lift modules (VLMs) offer greater efficiency, better space utilisation, and reinforced security for stored items compared to vertical carousels (VCs).
Here’s how they compare:
Definition
Vertical carousels (VCs) feature a series of carriers fixed to a chain drive. A motor rotates these carriers in a vertical loop along a track, moving both forwards and backwards, much like a Ferris wheel.
On the other hand, vertical lift modules (VLMs) are storage systems with two tray columns and a central elevator that moves vertically to access and automatically deliver trays to your warehouse operators.
Width and Height
Both technologies cover similar widths, so this isn’t a significant differentiator. However, vertical lift modules are roughly twice as deep as vertical storage carousels, giving VLMs a slimmer footprint.
Keep ergonomics in mind. It’s important that trays aren’t too deep, so your warehouse operators can easily reach items without getting strained.
Vertical lift modules typically measure five to 15 feet wide and seven to 10 feet deep. Their storage trays range from four to just over 13 feet wide and two to three feet deep, with a maximum product height of just over 28 inches.
In contrast, vertical storage carousels usually span six to 13 feet in width and four to just over five feet in depth, suited for smaller products. Their carriers for inventory range from four to nearly 12 feet wide and 16 to 24 inches deep, with product heights up to 18.5 inches.
Balancing Requirements
Vertical carousels require careful balancing to avoid an uneven distribution of weight across the trays.
On the other hand, vertical lift modules operate without this balancing requirement. This design eliminates the risk of overloading a single tray, thus enhancing the system’s overall stability and safety.
Accessibility
Vertical carousels require moving the entire set of shelves to access items, which can hinder productivity and efficiency.
Alternately, vertical lift modules enhance efficiency with an automated system that swiftly locates and retrieves items without moving the entire structure. This significantly decreases retrieval times and boosts productivity.
Installation
Vertical carousels, with their single-piece end frames, are less flexible and more challenging to install. This often requires up to four days to set up due to their cumbersome nature.
However, a VLM’s modular components can be easily transported and assembled — typically within just two days.
This efficient setup minimises downtime and enables adaptable configuration in various spaces, facilitating quicker operational integration.
How Do Vertical Lift Modules (VLMs) Work?
Vertical lift modules leverage various mechanisms to automatically deliver inventory to the warehouse operator:
1.When your warehouse employee needs an item, they enter the SKU details into a computer interface. The VLM control system, integrated with a warehouse management system (WMS), then calculates the most efficient retrieval path.
2.The inserter/extractor travels to the specific tray, retrieves it, and delivers it to an access opening or delivery bay for the employee to pick up the item.
3.More advanced VLMs also feature multiple access points. This allows several employees to simultaneously retrieve items, further reducing wait times.
4.The module then returns the tray to its original position.
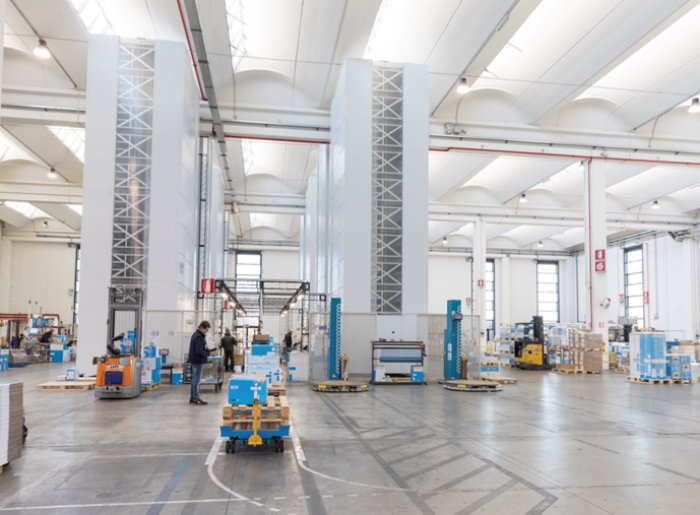
Vertical Lift Module (VLM) Options and Accessories
The vertical lift module’s versatility allows for straightforward integration with additional technologies, maximising its potential.
Key technologies include:
Augmented vision: This technology guides operators directly to the pick location, quantity, and item verification
Autonomous mobile robots (AMRs): AMRs can transport items or trays to subsequent workstations or to VLMs for order completion
Integrated robotics: Robotic arms can prevent human errors in the picking process
Warehouse management system (WMS): Track inventory levels, manage orders, and oversee picking processes in your warehouse
Pick-to-light systems: Achieve accuracy levels over 99.9% while boosting productivity
Temperature controlled atmosphere modules
Clean room applications
Conveyors, weight scales, scanners, label printers, barcode readers, RFID, tray accessories, and other innovations
Top 5 Reasons To Adopt Vertical Lift Modules (VLMs) for Your Modern Warehouse
Here’s how these advanced systems can transform your storage and retrieval processes:
1. Boost Storage Density
Vertical lift modules optimise space by storing items vertically, substantially increasing storage capacity without expanding the warehouse footprint.
At Modula APAC, the trays in our modules are designed to accommodate heavy loads effortlessly.
2. Improve Picking Speed
Vertical lift modules save you time in picking items because you only wait for the specific tray holding the item, not the entire set of trays. With a wide range of visual aids, such as laser pointers that indicate the location of needed items, vertical lift modules enable faster and more accurate retrieval for your operators.
Our VLMs deliver picking rates that exceed 300 lines per hour.
3. Secure Your Inventory
Vertical lift modules reinforce security measures by enclosing inventory and making it accessible only to authorised staff. Security features include controlled access points, user authentication, electrostatic discharge (ESD) protection, and an automatic door.
These measures reduce the risk of theft and damage, ensuring valuable items are protected.
4. Increase Employee Safety
A recent study identified a direct link between workplace fatigue and injuries.
Warehouse operators who frequently reach high and low to store and retrieve items face a prevalent risk of injuries.
Vertical lift modules automate the retrieval and storage processes, reducing the need for employees to participate in potentially dangerous activities like climbing or lifting heavy objects.
5. Decrease Labour Costs
Automation reduces the manpower needed for storage and retrieval tasks, cutting labour costs.
An example? Rather than multiple employees manually locating and transporting items, VLMs efficiently handles these tasks, enabling a single operator to manage the process from a central control station.
6. Get a Quick Return on Investment (ROI)
The efficiency gains, labour savings, and increased security from vertical lift modules often lead to significant cost savings. Businesses can recover their initial costs by streamlining operations and minimising overheads.
Integrating a Modula VLM into your warehouse operations typically yields an ROI within six to 18 months.
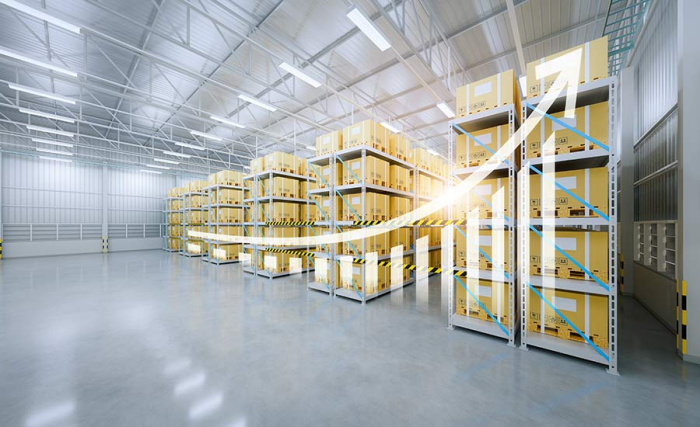
Discover State-of-the-Art Vertical Lift Modules (VLMs) at Modula APAC
At Modula APAC, we recommend transitioning from vertical storage carousels to our more efficient and adaptable vertical lift modules.
VLMs offers a more space-efficient storage solution by capitalising on ceiling height to maximise space utilisation in your warehouse.
Our units enable easy access for warehouse operators to a substantial inventory of goods, all stored within a secure and safe module. Items are effortlessly delivered to operators with a simple touch on the intuitive Copilot controller or by scanning a barcode.
Our vertical lift modules include:
Modula Lift: The Modula Lift can reclaim up to 90% of warehouse floor space, amplify work efficiency by two to three times, and boost picking accuracy to nearly 100%.
Modula NEXT: The Modula NEXT includes a uniquely designed bay that opens exclusively for a specific compartment during picking, eliminating the possibility of picking errors or item loss, thus ensuring high efficiency in your warehouse.
Modula Slim: The Modula Slim is ideal for storing loose materials and small parts, such as containers (think bins, boxes, cartons, and cases,) bottles, and coils.
It’s time to ditch vertical storage carousels.
A Quick Recap on Vertical Lift Modules (VLMs) for Modern Warehousing
If you’re considering an automated storage and retrieval system, it’s crucial to determine which system best suits your material handling process.
In summary, a vertical lift module surpasses a vertical carousel in terms of picking accuracy, security, and speed.
With no limitations on depth, height, and product variety, VLMs provide greater flexibility and capability, along with improved ergonomics.
At Modula APAC, we can help you reevaluate your storage solutions with our cutting-edge vertical lift modules.
Magnify productivity in your warehouse, ensure precise picking, and make sure your warehouse staff are safe while keeping your operations up and running.
Leave A Comment